Specialist Packaging Machine Repair Service to Keep Your Equipment Running Efficiently
Specialist Packaging Machine Repair Service to Keep Your Equipment Running Efficiently
Blog Article
Comprehending the Key Parts and Repair Work Techniques for Product Packaging Machine Upkeep
Efficient maintenance of packaging devices depends upon a complete understanding of their crucial components, consisting of the frame, drive system, and sealing systems. Acknowledging usual upkeep concerns, paired with the implementation of preventative strategies and repairing strategies, can substantially boost equipment integrity. Furthermore, the option of fixing methods, including making use of OEM components and the relevance of certified professionals, plays an important function in reducing downtime. To really comprehend the ins and outs of these systems and their upkeep, one must take into consideration the wider implications of ignoring these vital methods.
Key Elements of Product Packaging Makers
Product packaging devices contain several essential parts that interact to guarantee effective and effective packaging procedures. At the core of these makers is the structure, which provides architectural stability and houses the numerous operating components. The drive system, frequently a mix of gears and electric motors, promotes the movement of elements, allowing exact procedure throughout the packaging cycle.
An additional important part is the conveyor system, which transports items with different phases of the product packaging procedure. This is often matched by sensing units and controls that keep track of the placement and rate of products, making certain synchronization and minimizing mistakes. The loading system is essential for precisely giving the ideal amount of item into plans, whether in liquid, powder, or solid kind.
Sealing mechanisms, including warmth sealants or glue applicators, play a crucial role in safeguarding bundles, avoiding contamination and expanding service life. Furthermore, classifying systems are important for offering required product details, guaranteeing compliance with laws. The control panel, outfitted with straightforward interfaces, allows drivers to take care of device functions, screen performance, and make modifications as needed, making certain optimal efficiency and effectiveness in packaging procedures.
Common Maintenance Concerns
Reliable procedure of product packaging devices relies heavily on normal maintenance to prevent common problems that can interfere with production. Among these concerns, mechanical deterioration prevails, particularly in components like conveyors, motors, and seals, which can cause unanticipated downtimes. Additionally, misalignment of components can cause inefficient operation, creating products to be improperly packaged or damaged during the process.
Another typical maintenance issue involves the build-up of dust and debris, which can disrupt the machine's sensing units and moving parts. packaging machine repair service. This not only affects performance yet can additionally present safety and security risks. In addition, lubrication failings can lead to raised rubbing, resulting in overheating and ultimate element failure.
Electric problems, usually originating from loosened connections or worn-out wiring, can interrupt equipment functions, bring about substantial production hold-ups. Lastly, software application glitches as a result of incorrect setups or obsolete programs can hinder the device's procedure, necessitating immediate intervention. Resolving these usual upkeep problems proactively is essential for ensuring ideal efficiency and longevity of packaging machinery.
Preventative Maintenance Approaches
Executing preventative maintenance techniques is important for sustaining the efficiency and integrity of product packaging view website devices. These strategies incorporate a systematic approach to upkeep, concentrating on the routine inspection and servicing of devices to preempt prospective failings. By adhering to a set up upkeep program, drivers can determine deterioration on elements prior to they result in significant malfunctions.
Crucial element of a preventative maintenance approach consist of routine inspections, element, cleansing, and lubrication substitutes based upon producer suggestions. Utilizing checklists can streamline this procedure, making certain that no essential tasks are forgotten. Additionally, maintaining accurate records of upkeep tasks aids in tracking the maker's performance in time, helping with educated decision-making concerning future maintenance requirements.
Educating personnel on the importance of preventative maintenance enhances conformity and cultivates a culture of proactive care. Applying a predictive upkeep element, utilizing information analytics and sensing unit technology, can even more maximize machinery performance by predicting failures other prior to they happen.
Troubleshooting Methods
When encountered with breakdowns or inadequacies in product packaging devices, employing methodical troubleshooting techniques is crucial for recognizing and resolving problems swiftly. The primary step in reliable Recommended Reading troubleshooting is to establish a clear understanding of the device's functional specifications and efficiency metrics. This entails assessing the equipment's specs, along with any kind of mistake codes or alerts shown.
Following, operators ought to perform an aesthetic assessment, checking for noticeable indicators of wear, damage, or misalignment. This usually consists of analyzing belts, sensing units, and gears to identify prospective causes of malfunction. Gathering functional data, such as manufacturing prices and downtime logs, can additionally give understandings into reoccuring problems.
Once prospective issues are recognized, using a logical method to isolate the origin is critical. This may call for testing private elements or systems in a regulated fashion. Participating in conversations with drivers that communicate with the machinery consistently can produce valuable comments regarding uncommon habits or patterns.
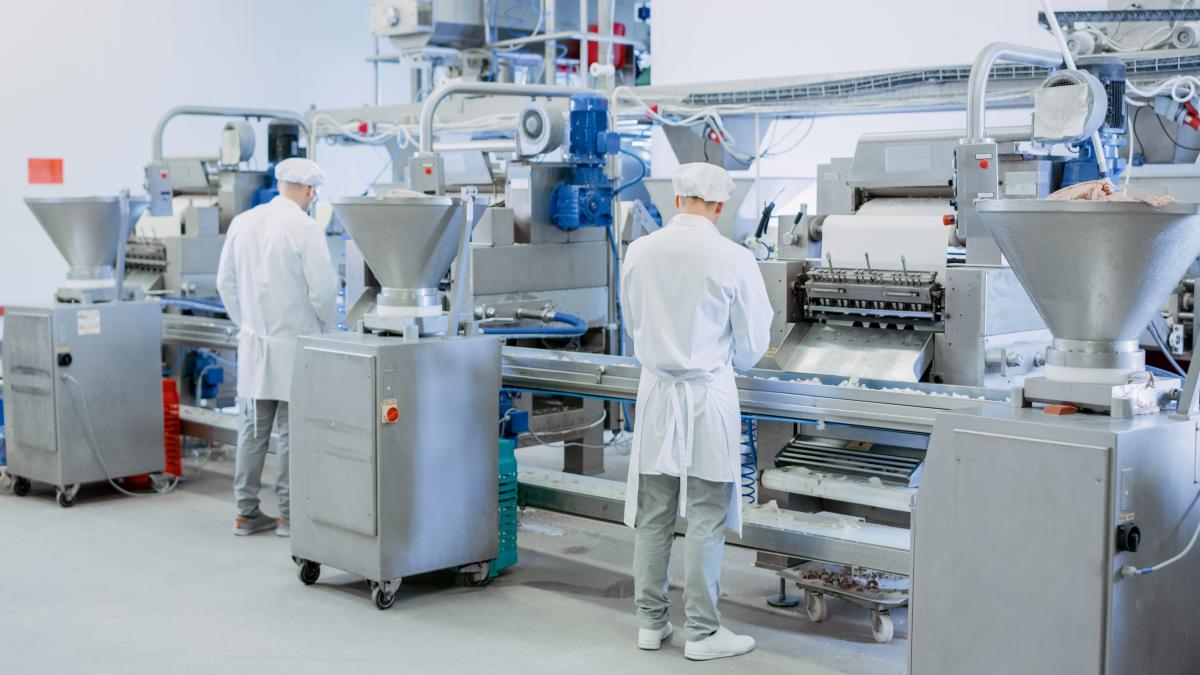
Repair Service and Substitute Ideal Practices
An extensive understanding of repair work and substitute ideal techniques is crucial for keeping the durability and performance of packaging machines. Consistently assessing the condition of maker components permits timely treatment, protecting against even more significant problems that can lead to expensive downtimes.
When repairs are necessary, it is vital to make use of OEM (Original Equipment Manufacturer) parts to ensure compatibility and performance. This not only preserves the integrity of the equipment but also supports service warranty contracts. Furthermore, it is a good idea to preserve a stock of vital extra components to promote fast substitutes and decrease operational disruptions.
For complicated repairs, engaging certified specialists with specialized training in product packaging machinery is advised. They have the experience to detect problems precisely and carry out repair services effectively. Moreover, documenting all repair work activities and components replacements is important for preserving an extensive maintenance background, which can assist in future troubleshooting.
Finally, applying a positive technique, consisting of regular assessments and anticipating maintenance methods, enhances the integrity of packaging equipments. By sticking to these ideal methods, organizations can make sure optimal device performance, lower operational dangers, and extend tools life-span.

Verdict
In verdict, a thorough understanding of product packaging maker components and reliable maintenance approaches is essential for optimal performance. By executing these methods, organizations can make sure the longevity and effectiveness of packaging makers, inevitably adding to enhanced functional performance and reduced prices (packaging machine repair service).
Effective maintenance of packaging machines hinges on an extensive understanding of their essential elements, consisting of the structure, drive system, and securing mechanisms.Efficient operation of packaging makers depends greatly on regular maintenance to prevent common problems that can disrupt production.Carrying out preventative maintenance methods is important for maintaining the effectiveness and integrity of product packaging machines. Furthermore, preserving exact records of maintenance activities help in tracking the device's performance over time, assisting in informed decision-making pertaining to future maintenance demands.
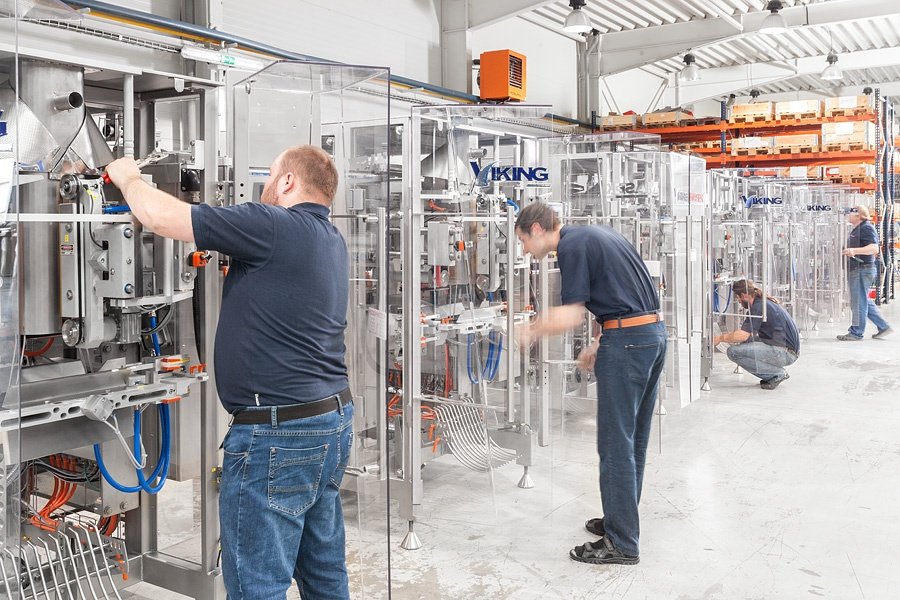
Report this page